With initial research done in metals recycling, the group was able to move onto more specific research, looking into subjects that appear promising to the end goal of identifying methods of improvement for the current recycling process. After reviewing different reports on the main points that either have a large amount of emissions or consume large amounts of energy, I focused on the disassembly and extraction steps of waste printed circuit board (WPCB) recycling.
The disassembly of a WPCB is the first step of the recycling process, involving breaking the whole circuit board into small particles, turning it into powder. The typical method to do so is to put the WPCB through a grinder, but I found that this technique has significant drawbacks. While grinding is effective for rigid and brittle material such as stone, WPCBs, with a high amount of organic compounds, have high relative ductility, allowing it to stretch and bend in ways an optimal grinder material can’t. This ductility makes it so that one pass through the grinder isn’t enough to reach the desired particle size, thus requiring a cycle of grinding until the desired result is achieved and greatly increasing the energy consumption of the process. In order to solve this, I researched two paths that would be able to address the ductility of the organic compounds. One method was to treat the WPCBs before grinding to decrease the ductility of the materials and was typically done by supercooling the shredded WPCBs in liquid nitrogen, thus making the materials brittle. Another method used can also be applied to the extraction step: the usage of supercritical fluids as a solvent.
Supercritical fluids are compounds that have reached above a certain temperature and pressure, called the critical point. When above this critical point, the material does not exist as a liquid, nor a gas, but a hybrid phase of both liquid and gas. Supercritical fluids are denser than gas but less dense than liquid, allowing it to demonstrate properties of both phases, which can make certain supercritical fluids excellent solvents. In the disassembly step, I found that the use of supercritical water can substitute the grinding process by causing a fast-acting oxidation reaction with the organic compounds found in WPCBs, dissolving the organic materials into a non-hazardous product and leaving the inorganic metals alone. Similarly, the extraction step, which involves obtaining the metals from the solutions made during the recovery step, can also use supercritical carbon dioxide with a co-solvent to create easily extracted metal oxides. Even better, there are methods documented to recover both the carbon dioxide and co-solvent after the process. Although promising due to the lack of harmful emissions and longevity of materials required for the reaction, the use of supercritical fluids has some problems, primarily in the corrosion of equipment and cost of energy. After researching the process, I found that as a supercritical fluid, both water and carbon dioxide exhibit corrosive properties for metals, which would lead to either specialized corrosion-resistant equipment or regular replacement of corroded parts. In addition, the supercritical temperature of water is approximately 374 degrees celsius, which when combined with the specific heat of water (4,184 J /kg ℃) means a significant amount of energy must be used to get water to the desired temperature. I am currently looking into methods of efficiently heating large amounts of water to increase this method’s viability on an industrial scale.
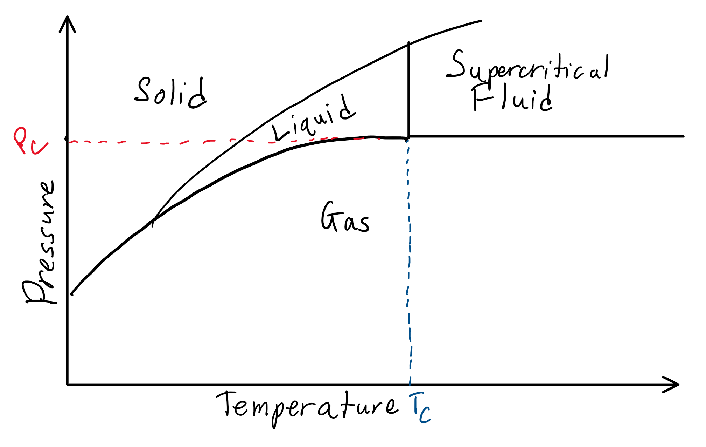